(This article was first emailed on May 17th, 2021 to fans who had registered an interest in finding out more about our Tricorder.)
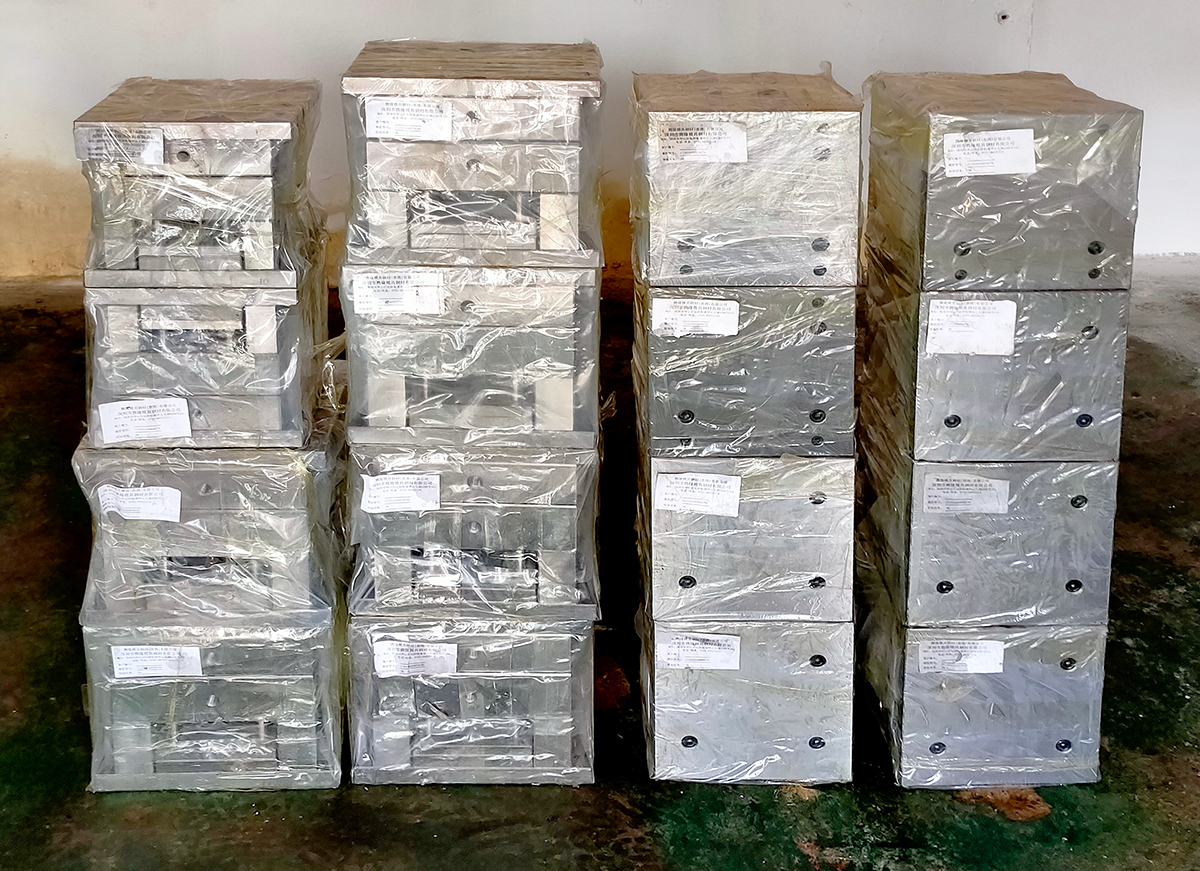
The tricorder is made from a mix of different materials. Replicating the original as closely as possible, machined and extruded aluminium provide key design accents as well as the basic structure of the tricorder. Die cast zinc is used for the display stand, a stitched leatherette for the strap, and four different kinds of precision-engineered injection-moulded thermoplastics combine refined function, durability and aesthetic accuracy to complete the replica.
All the injection-moulded parts necessary to make a tricorder collectively weigh only 241g (8.5oz), but require two and a half tons of tooling to make them.
Sixteen mould bases weighing two and a half tons are needed to make the plastic parts of the tricorder
Sixteen large mould bases, each weighing 80 – 250 kg (175 – 550 lbs), of pre-hardened S136H stainless steel, are carved out using intricate and highly accurate mechanical machining, electrical discharge machining (EDM) and hand-finishing processes to create the 68 cavities that are needed to produce every tricorder.
Toolmaking to produce high-quality, highly toleranced parts is a complex and time-consuming process. The tools not only need to have perfectly machined and finished cavities, but also need an intricate system of location pins, ejectors, molten plastic feed tubes (sprues, runners and gates) and a network of internal channels through which cold water is pumped to cool the mould as rapidly as possible during each injection moulding cycle.
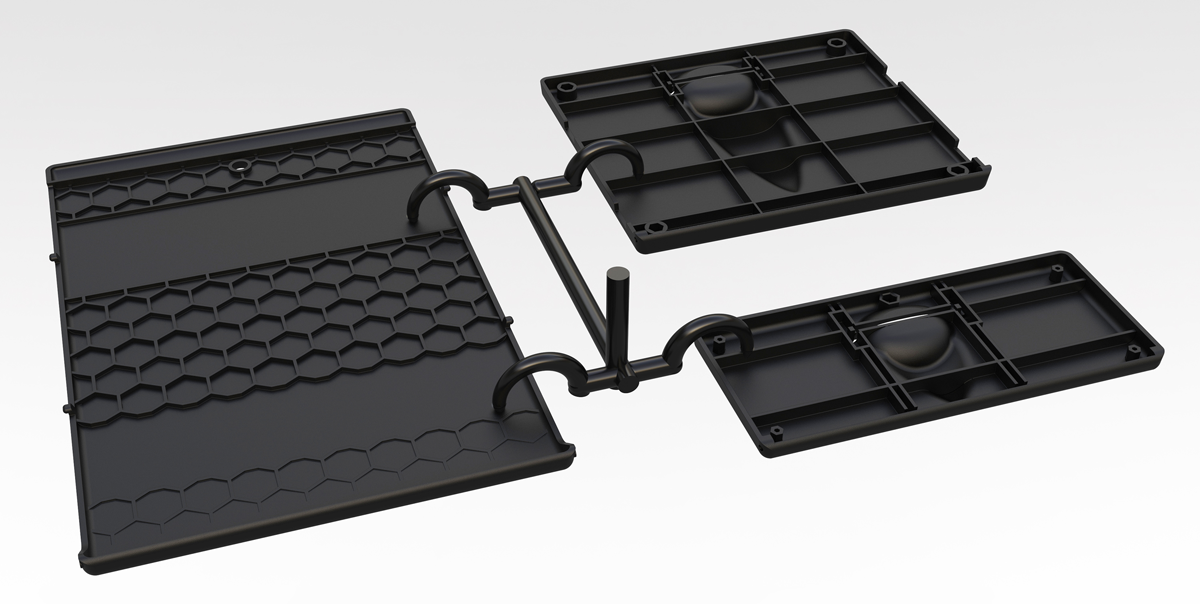
Cashew gates, typically used to get the injection location behind a “show” surface, are carefully positioned to ensure the most even flow and reliable fill.
The design of the mould tool is more than just making a perfectly shaped cavity. To make sure the inlet gates are perfectly placed, and tool temperatures and injection pressures are all optimised, powerful simulations are used to model the dynamics of the molten plastic flow to ensure that the resulting part is smooth, repeatably accurate with minimal shrinkage, and doesn’t experience extreme temperature gradients that would build stresses into the part or result in scorch marks (too hot) or weld lines (where two cooling fronts of plastic meet) during the moulding cycle.
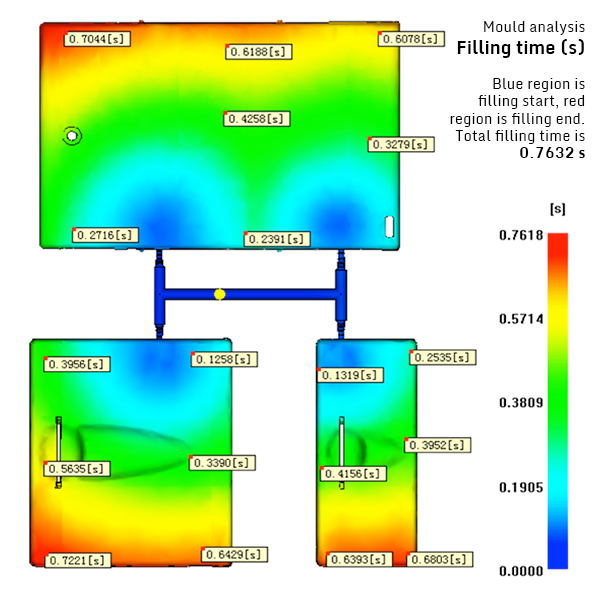
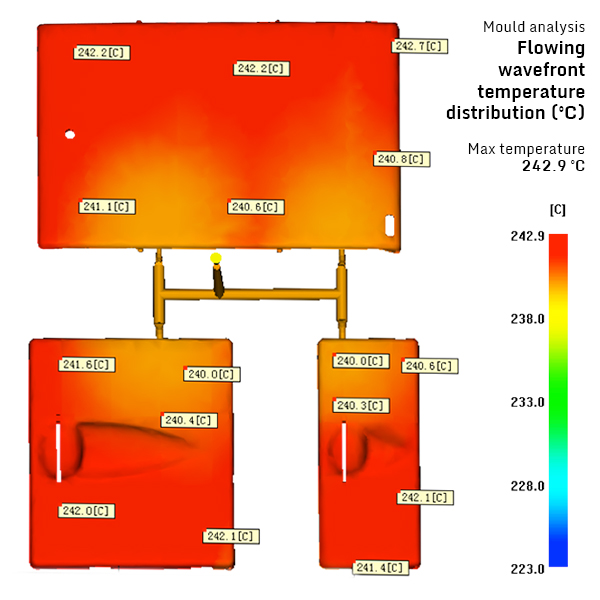
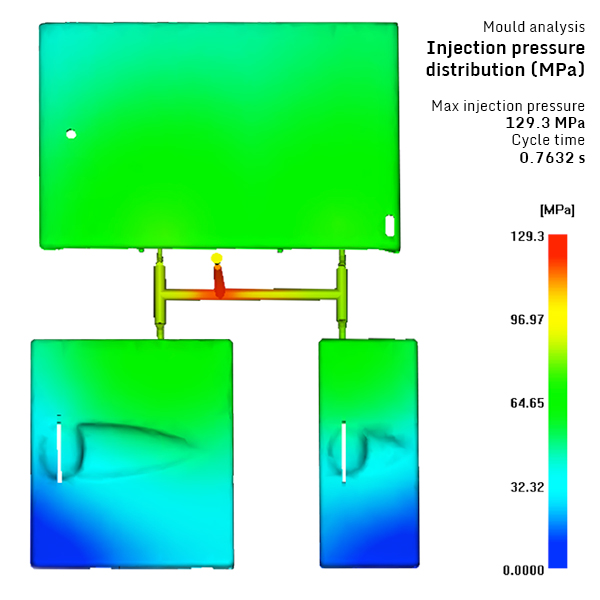
Detailed analysis of each mould tool is carried out to assess mould performance and ensure that the gates are of the right type and positioned optimally so that the resulting parts can made without faults
Molten plastic is injected into the mould under enormous pressure. To stop it leaking out of the tool at the join between the two halves of the mould, and thus creating unsightly flash, the mould must close very accurately and securely. As larger parts require more pressurised plastic to fill them, an injection moulding machine’s closing pressure, measured in tons, determines the size of the part that can be produced on that machine. For the largest tricorder component, the back panel, which will be moulded in the same tool as the two doors, the moulding machine has a closing force of 160 tons.
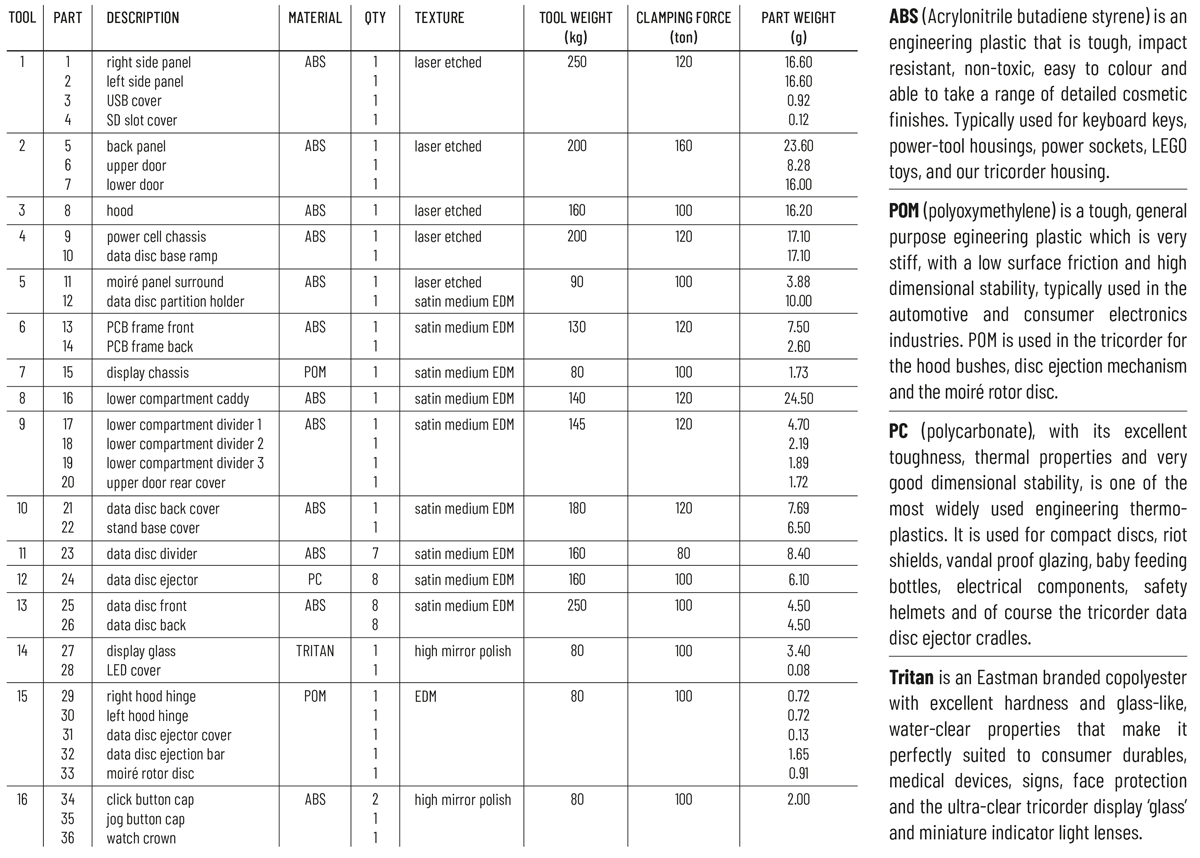
Sixteen tools are required for the tricorder’s 68 injection-moulded components
Injection moulding tools are made in a multistage process. The tricorder mould bases were milled to give them a perfectly flat surface, after which a CNC (computerised numerical control) machining process was used to rough out the basic shapes of each mould. Eleven different milling cutters with a range of tip shapes and diameters are needed to machine out the basic tool shapes.
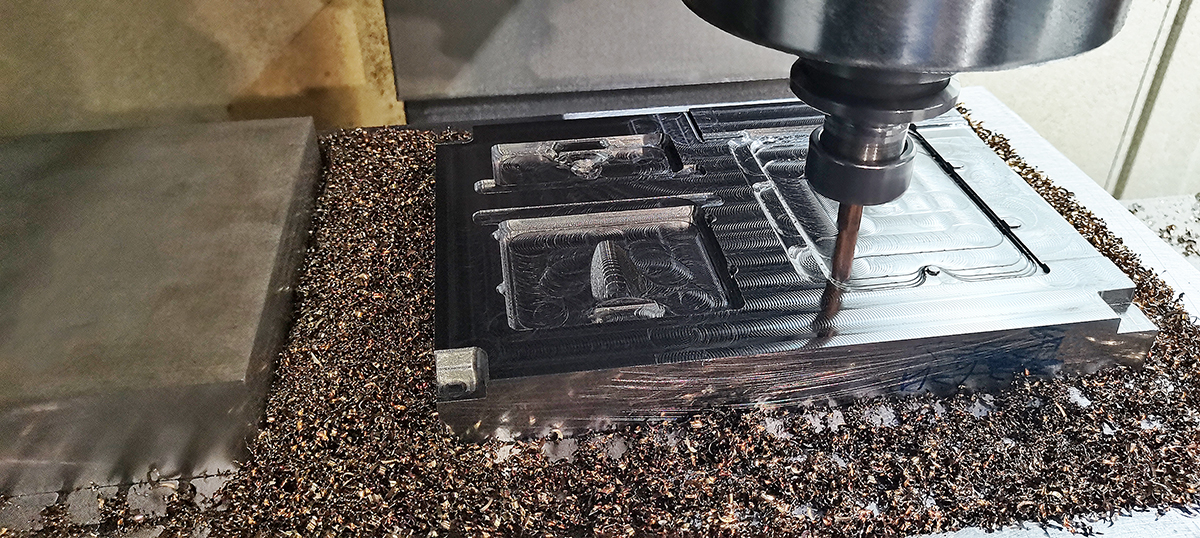
Eleven different milling cutters are needed to rough out the tool shape before the tool is heat-treated to harden it
The tools were then heat-treated to increase their hardness before the shapes were refined by CNC machining with smaller milling cutters to get closer to the actual geometry of the parts. To complete each cavity’s form an EDM (electrical discharge machining) process is used.
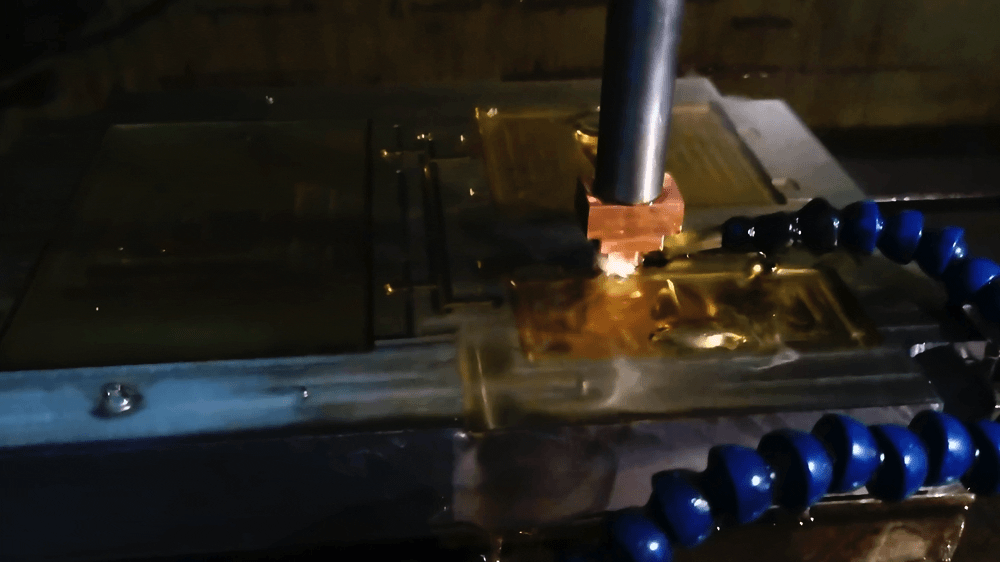
High voltage causes electrical arcs across the small gap between a copper electrode tip and the tool face vaporising tiny chunks of the tool surface to erode it away in the shape of the pattern.
Often referred to as spark erosion, the process literally erodes the surface of the tool with high voltage arcs, created between the surface of a fine wire or copper pattern and the inner face of the tool, vaporising minute chunks out of the surface of the tool as the wire or pattern is slowly pushed into it, submerged in a dielectric oil bath. EDM leaves an even, microscopically-pitted surface that, depending on the strength of the voltage applied, results in anything from a coarse granular-looking surface to a smooth satin finish.
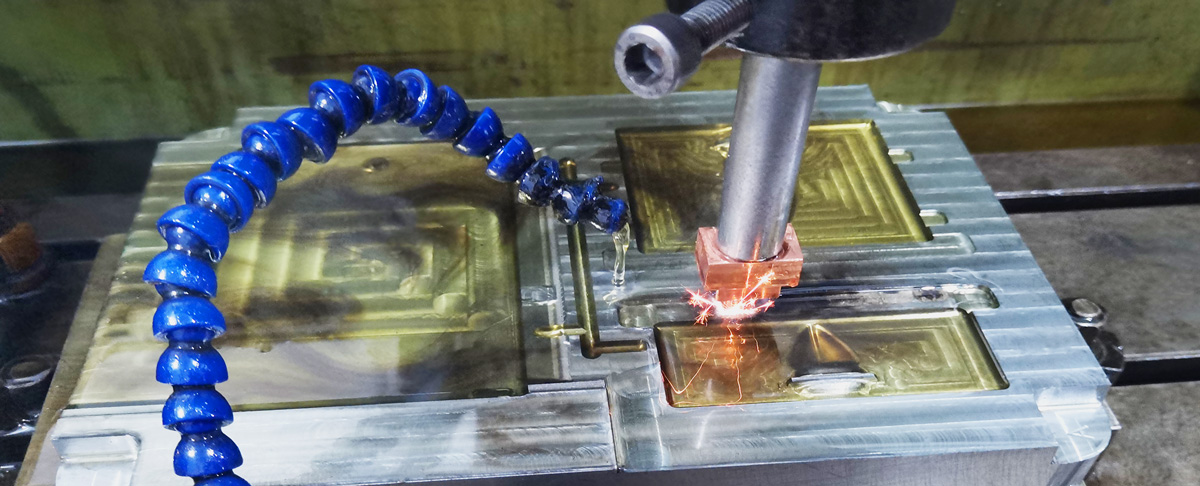
The cavity for the tricorder back panel and both front doors emerges from the tool base.
Once the tricorder tools have completed this stage they will be tested. The complex tools are assembled and fitted to injection moulding machines so that a series of “first-shot” mouldings can be produced. The fit and finish is assessed and any issues can be addressed at this point, in a process called tool touch-up. It is relatively easy to remove metal from a tool if the touch-up involves making a feature bigger: these are referred to as “metal-off” changes. But if a part of the resulting moulding needs to be made smaller, then the more difficult process of a “metal-on” change requires new metal to be welded into the tool and once again machined or spark-eroded away with a new copper pattern to create the revised geometry.
When we are happy with the mouldings, and are sure that they are performing well with each other and together with all the other metal and electronic components, the tooling will be textured to create the required surface finishes.
For many of the tricorder parts a medium satin finish has been specified, but for the screen ‘glass’, the LEDs, watch crowns and buttons, where a highly polished surface is required, finishing the tool continues by hand. Progressively finer diamond pastes are used to buff the inner surfaces of the mould to a near-perfect mirror-smooth finish. Finally, to ensure the surface is as smooth as possible, the inner surfaces of these tools are chrome-plated. For the exterior panels of the tricorder where the original replica was made from vacuum-formed Kydex, after polishing, the tools will be sent to the same specialist texturing company that created the surface finish for our Communicator, where they will have the distinctive Kydex pig-skin pattern laser-etched into the surface.
.
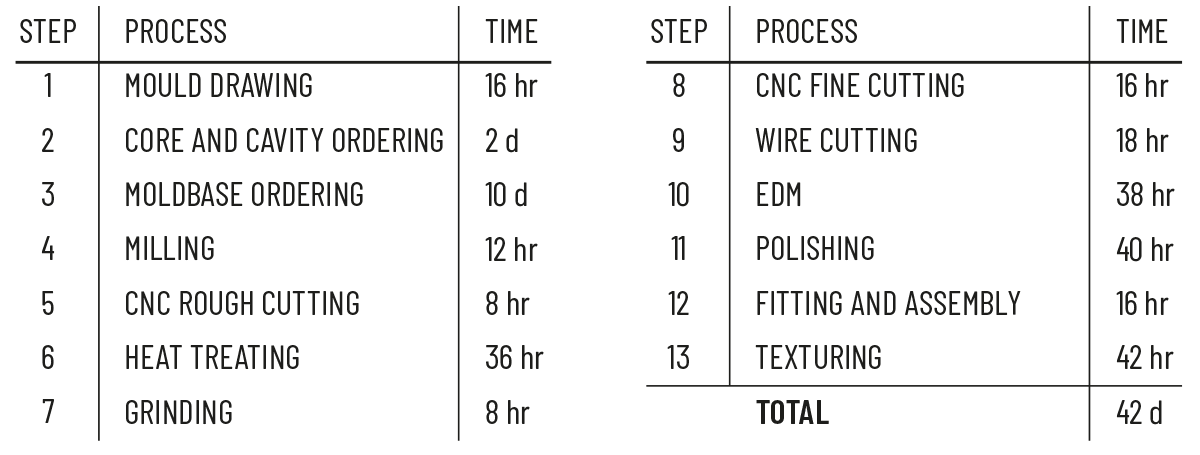
Every tool and each cavity has to go through a laborious and painstakingly accurate process in order to make the tricorder’s precision injection moulded parts.
Over the course of this project, replicating the tricorder hero prop has required the specialist skills and knowhow of a number of different engineers, powerful software, and some seriously heavy equipment. Yet still, at each stage the importance of expert hand finishing is evident. Even in the toolmaker’s workshop, surrounded by enormous computer-controlled milling machines and EDM spark eroders, hand polishing, fitting, and assembly account for almost 30% of the time it takes to make the tool. It seems that when making a replica, however, it is made, old-fashioned artisan skills are always needed to get the job done.
LLAP
Chris
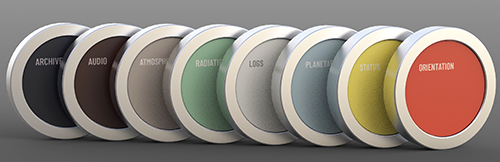
Coming next time
Data discs – what they do and how they work
Fans who register with us will be the first to read our news and the progress of this exciting Tricorder development and, later, where and when to purchase it. You can catch up with the story so far here on this blog, but if you haven’t already done so, why not register your interest in the Tricorder – you’ll then receive a personalised registration certificate and early access to these updates (before we publish them on our website).
Hello Chris and Richard. I like the new color palette on the data disks. Looking forward to your next update!
jim
I heartily agree with Jim. The new color palette is a *marked* improvement on both the original rendering colors *and* the last set of colors chips you were considering. These definitely feel more ‘Starfleet’ (switch/data tape colors). Thank you!
Yes! Though we never saw them, I can totally buy this is what they would have looked like. Feels right at home with the device.
Back to the subject of this blog, I’m in the aircraft manufacturing industry and the program I’m on has several injection molded parts. Reading your blog made me feel like I was in a production meeting with our supplier. We had a part where two wavefronts weren’t merging properly and caused a weld line that was weak and splitting open during installation of the part. We had to add gates to control the flow of the wavefronts and eliminate the weld line. Very complex and expensive processes.
When I was in high school, I was in an Industrial Plastics program where I learned about this.
When I was in high school, Star Trek was in its first syndication on TV, an episode showing each day, and I was inspired to (poorly) hand-make my own props, to take to science fiction conventions.
Now, almost 50 years later, I’m taken back by seeing both of the interests of that day resurrected together. Thanks!
Just found out Monday is a bank holiday in the UK again, so we have to wait till Tuesday for the next update, which is wreaking havoc with my withdrawal symptoms. Must… not… pull… my hair… out… 😛
Don’t worry, the next post is locked and loaded and will be emailed out on Monday.
YAAAAAAAAY!!!!! That’s great news, because I’m already missing a lot of hair. 😛
Looking forward to it! 🙂
Hallo Chris and Team,
in Germany, TOS came on TV for the first time at the beginning of the 70s and I probably only watched it because my father was interested in SF films.So Star Trek and especially TOS were the first films that got me excited about SF and still do today. I was never someone who collected many models, but with Star Trek it is different. Now that I am approaching 60, only a few Star Trek models from TOS and “The Motion Picture” are left.Usually I only collected starship models. But with the release of the WAND replicas this has changed, so that I have bought everything that was on offer so far.I was very impressed by the functionality of the devices and of course I immediately thought that there should also be the tricorder, which fits in there in terms of quality.
Now it’s “almost” time and I’m very impatient to hold one of these in my hands and try out all its functions myself.
For many years I have been professionally involved in the production of plastic parts and I also worked for 10 years in the forging sector for the car industry. Therefore, I am familiar with many production processes. Many Products that have passed through my hands can or could be bought not only throughout Europe but also worldwide.At the moment I am working independently in the construction area with 3D scanner, CAD for reverse engineering, Milling, etc. and due to my many years of experience I can completely follow the construction process, which you describe in such detail in the newsletter, so that I actually wish to be present at the development process, which of course increases my impatience even more ;-).
But I have the consolation that the right people are involved.Some people would laugh about the effort for such a “gimmick”. But you have your heart in the right place, that you deal so intensively and seriously with the matter and defy all odds.Your hands have the talent and spare no effort to display all technical professionalism to create the best possible product and you give free rein to your creativity to get the most out of the smallest corner.
Therefore, I can only praise your effort from the bottom of my heart. Even if it sounds a bit theatrical. But that’s the way it is in my position.
Even though I am now always up to date with the newsletter. In Germany, the things were always hard to get. So please don’t forget to “bless” us here on the other side of the planet with large quantities. Or I can send you my address. Shipping costs are totally irrelevant. But it would be a disaster if I couldn’t get this genius tricorder to hold in my own hands.
Only the best for you.
Greetings from the only city in the world with its own “Made in” trademark. 😉
Ralf
How I feel? “young, – I feel young” 🙂
Got the latest email about the discs! Wonderful info and breakdown of the functions. You really crammed a LOT of capabilities into this little space! I’ll save any discussion of those specific functions for the thread here dedicated to them next week. But I do want to ask a broader question – one MANY are wondering about – which has been prompted by the new information:
I know you have established that there will be no video *recording* capabilities. As I’ve mentioned in the past here, that makes sense. It would be like trying to record images and video with your smart watch – not very conducive to the capture of good visual data. But I noted in in the email’s functions databaset absolutely *no* mention of video *playback* capabilities whatsoever. In all the descriptions, there is reference to “images and data”. But, unless by images you mean “moving images” as well as “still images”, it sounds like your Tricorder will have *no* video capabilities whatsoever.
Is that true? (I *hope* not!) Or is video playback one of the other functions you allude to when you write: “Our tricorder does more than just sense and record data from the environment”?
I’m not necessarily asking you to go into details here if that IS one of the other functions to which you are alluding. As you say, IF video playback IS another of the functions of the Tricorder, you will ‘explore that capability’ “in detail in future posts”. It’s just that video playback is one of the *only* true functions of the Tricorder we have ever seen on-screen. Given that fact, I am sincerely hoping that such a *vital* ‘canon’ function is included in your “replica”. It’s absence in a professionally-built product would be especially disappointing, given the fact that function is usually included in the Tricorders made by the better *amateur* prop/builder fans these days.
Richard and Chris, I don’t feel I have the right to speak on behalf of all fans, but . . . As a fan of the show since 1966-67 (I was a child then, inspired by a future that “might be”) I look at this installment as a man in his 60’s and am so thankful to have lived to see this day. You have restored my childhood days, with your attention to details, your commitment to quality, and most importantly your obvious love for the art inherent in Star Trek’s Props. For this and so much more, I thank you deeply and applaud your efforts with profound appreciation. Bravo gentleman! Your description of this intricate process is evidence that this project will be part of a legacy for all Fans to proudly be a part of soon.
Rauel, thank you so much for your enthusiasm and all your kind words, as fans ourselves we feel honoured to be able to bring this epic prop to life.
Just make it cool. I know that you will.
Just make it awesome. I know that you will.